Aktualności
Biogazownia przy fabryce syropów (16709)
2014-01-17Amerykański koncern Cargill uruchomił biogazownię rolniczą na terenie swojej fabryki w Bielanach Wrocławskich w czerwcu 2012 r. Ta biogazownia jest stosunkowo niewielka, ale dzięki zastosowaniu innowacyjnych rozwiązań zalicza się ją do najciekawszych w Polsce.
Zakład produkcyjny firmy Cargill w Bielanach Wrocławskich zajmuje się przetwórstwem pszenicy. Z zawartej w mące pszennej skrobi produkowane są syropy glukozowe i fruktozowe, czyli półprodukty służące do słodzenia m.in. napojów i słodyczy. Pozostała część, pochodząca z mielenia i przetwórstwa zboża, stanowi surowiec do produkcji etanolu, tzw. glutenu pszennego witalnego oraz pasz zwierzęcych.
Zakład od początku swego istnienia prowadził własną oczyszczalnię ścieków. W miarę, jak się powiększał, ilość ścieków rosła. 10 lat temu na terenie fabryki powstała biogazownia, wyposażona w technologię beztlenowego przetwarzania płynnych resztek pszennych na biogaz – tzw. bioreaktor. Technologia SGBR (tak nazywa się reaktor beztlenowy, o którym mowa) ma za zadanie przetwarzać strumień wód potechnologicznych najbardziej obciążonych resztkami organicznymi. Dzięki 80-90 procentowej redukcji ilości biomasy w tych wodach, bioreaktor wspomaga pracę oczyszczalni. Bakterie metanowe, żyjące w reaktorze beztlenowym, doskonale sobie radzą z wysokimi stężeniami ChZT (rzędu 10kg/m3), czyli tzw. chemicznego zapotrzebowania tlenu.
Cykl pracy reaktora beztlenowego jest cyklem ciągłym – wody potechnologiczne w sposób ciągły trafiają do zbiornika buforowego, gdzie zachodzi wstępne skwaszanie materii organicznej. Następnie są podawane do systemu bioreaktora, gdzie jest stabilizowane pH. W wyniku kontrolowanej cyrkulacji przez granulowane złoże bakterii w reaktorze, zachodzi fermentacja beztlenowa – bakterie rozkładają materię organiczną, przetwarzając ją do biogazu. Strumień cieczy opuszczającej bioreaktor jest kierowany do dalszego oczyszczania w zakładowej oczyszczalni ścieków.
Pierwszym pozytywnym efektem, jaki zaobserwowano po uruchomieniu bioreaktora, było znaczne zmniejszenie ilości produkowanych przez oczyszczalnię osadów ściekowych. Jednak produkowany w bioreaktorze biogaz nie był wykorzystywany i spalano go w tzw. pochodni.
Już na tym etapie uruchamiania biogazowni powstawały plany energetycznego zagospodarowania biogazu. Przeprowadzone analizy wykazały, że wytwarzany w bioreaktorze biogaz jest bardzo dobrym paliwem (zawiera od 65-84% metanu, resztę stanowi CO2 i N2). Na podstawie tych przesłanek firma Cargill rozpoczęła analizę opłacalności i wykonalności inwestycji polegającej na wykorzystaniu biogazu na cele energetyczne. Wśród rozpatrywanych wariantów pojawiały się propozycje m.in. spalania w kotle parowym, opalania biogazem suszarni paszy, zasilania biogazem mikroturbin generujących energię elektryczną. Ostatecznie w 2008 roku, najbardziej efektywnym rozwiązaniem okazał się projekt niewielkiej elektrowni, opartej o silnik spalinowy firmy Jenbacher, produkujący energię elektryczną i cieplną z biogazu.
Na etapie opracowania analizy zysków i strat pojawiło się zagadnienie zasiarczenia biogazu. Biogaz, pomimo stosunkowo nieskomplikowanego składu chemicznego, zawiera także zanieczyszczenia, które mogą go całkowicie zdyskwalifikować jako paliwo. Do takich zanieczyszczeń należy siarkowodór (H2S). Intensywnie śmierdzący i silnie toksyczny produkt procesów fermentacji biomasy jest źródłem wielu problemów technicznych i środowiskowych. W wyniku spalania paliw zawierających H2S, powstają tlenki siarki i kwas siarkowy. Powstające spaliny mają bardzo kwaśny charakter i stanowią silnie korozjogenne środowisko dla urządzeń, w których zachodzą procesy spalania biogazu. Spalanie nieoczyszczonego biogazu w silnikach prądotwórczych powoduje szybkie zużywanie elementów metalowych i częstą potrzebę wymiany oleju.
Zagadnienie oczyszczenia biogazu z siarkowodoru okazało się jednym z kluczowych zagadnień technicznych projektu. Po przeprowadzonej analizie ekonomicznej i porównaniu skuteczności dostępnych technik, firma Cargill zdecydowała się na inwestycję w system mokrego odsiarczania biogazu w urządzeniu BioSulfex® Zespołu Innowacyjnego PROMIS z Warszawy.
W 2012 roku zostały wygospodarowane odpowiednie środki do realizacji inwestycji. Przyjęto następujące założenia wydajnościowe dla jednostko kogeneracyjnej:
Moc elektryczna: 0,526 MW
Moc cieplna: 0,581 MW
Roczna wydajność elektryczna: 3,24 GWh
Roczna wydajność cieplna: 3,58 GWh
Jednym z przyjętych warunków budowy było założenie, że cała produkcja biogazu będzie oparta o surowiec pochodzący z przetwórstwa pszenicy w fabryce Cargill w Bielanach Wrocławskich. Do biogazowni nie dowozi się żadnego surowca z zewnątrz. Drugim założeniem było całkowite zamknięcie cyklu produkcyjnego, celem zapobiegania przykrym zapachom. Po trzecie prąd i ciepło produkowane z biogazu miały zasilać wyłącznie fabrykę, zmniejszając o kilka procent konsumpcję energii i gazu w fabryce (ciepło z jednostki kogeneracyjnej jest używane do technologii suszarni glutenu). Czwartym i kluczowym założeniem było odsiarczenie biogazu do poziomu, który umożliwi bezpieczną i bezawaryjną eksploatację jednostki kogeneracyjnej.
Spełnienie powyższych założeń stanowiło duże wyzwanie technologiczne i inwestycyjne, tym bardziej, że fabryka Cargill w Bielanach Wrocławskich usytuowana jest niedaleko węzła autostradowego oraz sąsiaduje z hipermarketami, z centrami logistycznymi, a do najbliższych domów jest około kilometra. Pomimo w/w przeszkód firma Cargill zdecydowała się na budowę zielonego źródła energii.
Zaproponowany jako najlepszy system odsiarczania Biosulfex® okazał się być wyjątkowo skutecznym w usuwaniu odorów i siarkowodoru. Od samego rozruchu redukuje stężenie siarkowodoru w biogazie z poziomu 20.000 ppm do zawartości poniżej 10 ppm. Katalityczna obróbka H2S sprawia, że cały siarkowodór jest konwertowany do siarki – niereaktywnej pulpy siarkowej. Dodatkowo znacznie obniża poziom zanieczyszczeń krzemianowych w biogazie.
Założenia produkowanej energii elektrycznej okazały się jednak zbyt wygórowane, ze względu na zmniejszenie ilości materii organicznej kierowanej do biogazowni na przestrzeni 2012 roku, wskutek oszczędności procesowych na wcześniejszych etapach przetwórstwa w fabryce. Mimo to, uzyskiwane ilości energii i ciepła stanowią ekologiczny wkład w funkcjonowanie zakładu Cargill.
Na przestrzeni 2012 roku pojawił się tylko jeden problem, którego natura nie leży w dziedzinie techniki. Podczas, gdy Cargill decydował się na budowę bioelektrowni, zielone certyfikaty kosztowały 240-250 zł za 1 MWh, a biogazowniom przyznawano żółte certyfikaty. Dziś te pierwsze kosztują ok. 200 zł (na początku 2012 roku ich cena spadła nawet do 100 zł), a cena tych drugich od kwietnia 2013 wynosi okrągłe zero. To sprawiło, że cała inwestycja będzie się zwracać dużo dłużej niż założono w biznesplanie.
Na pocieszenie można jedynie dodać, że dzięki zakwalifikowaniu tej instalacji jako biogazowni rolniczej, formalności związane z budową i rejestracją jednostki kogeneracyjnej były szybsze i łatwiejsze aniżeli w przypadku pozyskiwania koncesji na produkcję energii elektrycznej z Urzędu Regulacji Energetyki (URE). Zamiennie wystarczył wpis do rejestru Agencji Rynku Rolnego (ARR), którego uzyskiwanie trwa zazwyczaj dużo krócej niż otrzymanie koncesji.
– Musimy jednak nadmienić, iż zarówno w ARR, jak i w URE spotkaliśmy się z dość przyjaznym nastawieniem wobec naszej inwestycji. – mówi Zbigniew Kot z bielańskiej fabryki Cargill. – Dużym wsparciem okazały się dla nas władze samorządowe i wojewódzkie. Widać było, że naszym urzędnikom zależy na wspieraniu inicjatyw takich jak nasza. Dzięki ich cierpliwości i pomocy budowa "zielonej" elektrociepłowni w Bielanach Wrocławskich był możliwy i zakończył się sukcesem – dodaje Michał Łupiński, zatrudniony w Cargill.
Jacek Krzemiński
Niniejszy materiał został opublikowany dzięki dofinansowaniu Narodowego Funduszu Ochrony Środowiska i Gospodarki Wodnej. Za jego treść odpowiada Fundacja – Instytut na rzecz Ekorozwoju, poglądy w nim wyrażone nie odzwierciedlają oficjalnego stanowiska Narodowego Funduszu Ochrony Środowiska i Gospodarki Wodnej.
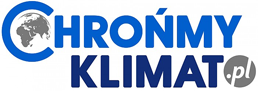
ChronmyKlimat.pl – portal na temat zmian klimatu dla społeczeństwa i biznesu. © Copyright Fundacja Instytut na rzecz Ekorozwoju
Redakcja: ul. Nabielaka 15 lok. 1, 00-743 Warszawa, tel. +48 +22 8510402, -03, -04, fax +48 +22 8510400, portal@chronmyklimat.pl